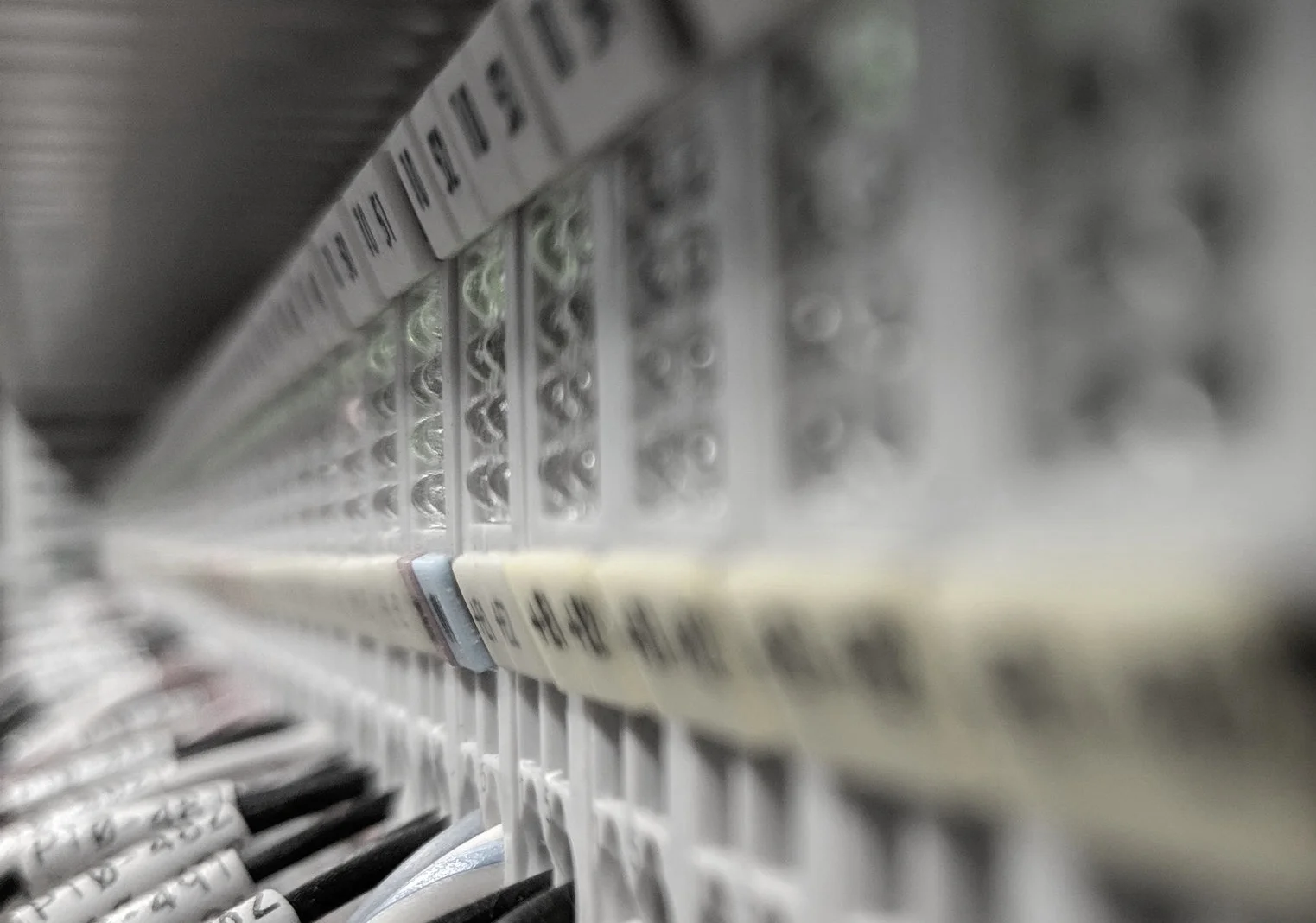
TOTAL SITE CONTROL
With our strong hands-on feed mill process experience, we recognized the need for high performance Pellet Mill control automation and developed the Progressor Pellet Mill Controller. This innovative and advanced system demonstrates an exceptional level of process monitoring, including pellet mill stability, throughput and temperature control.
Raising the bar to a new level of pelleting performance and intelligence
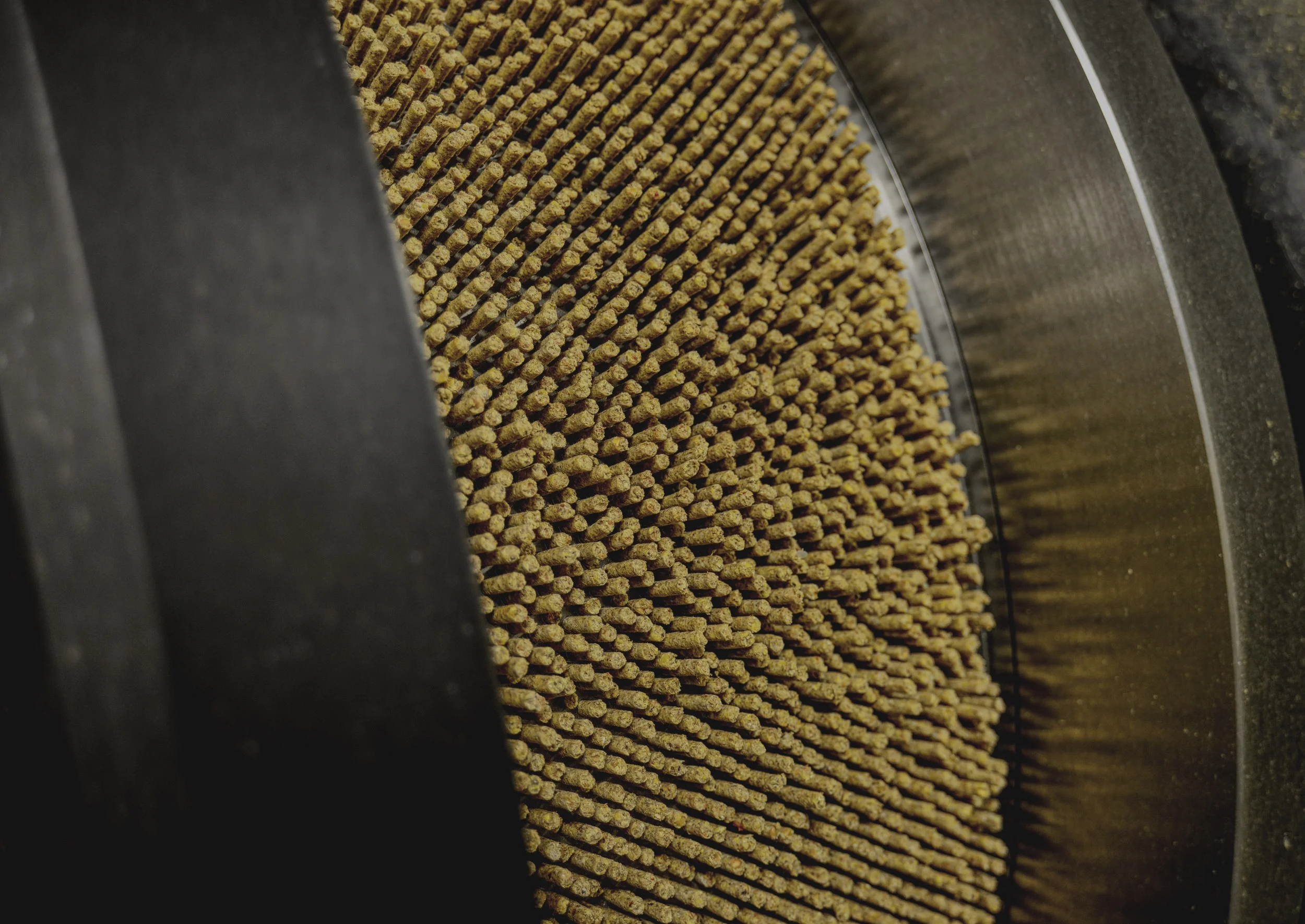
Receiving
+ Solid Product Receiving
- Auto Routing based on ingredient
- Commodity interlocking
- Bin high level interlock re-auto route to secondary bin
- Commodity based receiving speed
- All transactions are logged in the database, providing complete documentation for inventory, quality control and regulatory compliance.
- Custom ERP Integration*
- *Provided the ERP system has data transfer mechanism
- Inventory management
- Auto inbound commodity select based on inbound ticket Barcode or RFID
+ Liquid Receiving
- High level alarm
Grinding
Keep full-full scheduling
Auto schedule grinding runs to keep destination bins full based on usage
+ Hammer Mill Grinding
- Mill rate based on preset rate and current motor load
- Auto direction reversal on next start after preset run time
- Interlock and alarm on
- Vibration
- Bearing temp
- Grinding chamber temp
+ Roller Mill Grinding
- Mill rate based on preset rate and current motor load
- Rolling/Cracking
- Single roll pair adjusted to 1:1 ratio with VFD
- Auto adjust to preset roll gap
- All additional pairs are set to full open
- Grinding
- When utilizing Keep-full feature, feeder speed, motor load, and roll gap auto adjust to presets
- Grinder sampling and roll gap fine tuning
batching
Complete batch automation
Progressor has the capability to measure every product autonomously based on a predefined recipe up to 1gram** resolution
**Where the product is fed by a Camar HD Micro
All weighments are recorded for reporting
+ Order Interface
- Above
+ Manual Order Entry
- Order can be created from recipes in the event that the order interface is offline, or not implemented
+ Batch Sizes
- Progressor can be configured for 2 batch size modes:
- Automatically scale each batch to be of equal size
- Fix all batches to a set size except for the last batch which is used to complete the balance of the run
- Batch sizes are calculated based on each scale weight and volumetric capacity and will automatically reduce batch sizes for low density formulas as required to fit the scale.
+ Scale Optimizer
Progressor Scale Optimizer automatically determines the highest resolution scale to use for each ingredient based on the minimum batch amount configured for each scale. For example, some formulas require a small amount of an ingredient and some formulas require a large amount of the same ingredient. The same ingredient can be placed in a major scale bin, a micro bin, an HD micro bin and also be available as a Hand-add. Progressor calculates the inclusion rate of each ingredient then automatically batches this ingredient to the scale with the highest resolution and also has the required capacity. This powerful standard Progressor feature maximizes both flexibility and accuracy for your formulations.
Progressor is configurable as follows:
- Assign an ingredient to any scale exclusively, or
- Automatically assign an ingredient to any available scale based on the inclusion rate. Each ingredient has a configurable minimum batch amount per scale.
- Example Configuration:
- Ingredient A is in a major scale batching bin, a micro bin, as well as an HD micro bin.
- If the target batch amount > 10 Kg it is automatically assigned to the major scale.
- If the target batch amount = 0.4 to 10 Kg it is automatically assigned to the micro scale.
- If the target batch amount < 0.4 Kg it is automatically assigned to the HD micro.
+ Free-Fall Compensation
- Fixed Free-fall compensation mode
- Free-fall compensation parameter is adjustable, but remains as set
- Automatic Free-fall compensation
- Highly accurate dynamic free-fall compensation algorithm automatically tunes each batching auger free-fall parameter, drastically reducing jog times and increases accuracy
- Auto timed run feature calculates required batching auger run time for weighments less than the freefall amount based on historical data. This eliminates jogging for these weighments
- Historical performance log provides immediate reference to historical performance of a specific batching auger/slide to simplify parameter tuning decisions
+ Sequencing
- Progressor Sequencing is a powerful tool with fully configurable sequencing rules for specific ingredients and animal species. Progressor automatically tracks all products that have been through each stage of the process and prevents an order for a sensitive species from following any formula that contained a sensitive ingredient. Controlled products can be configured with both White List and Black List rules.
- For some controlled products, not only is a plain product run required to flush the system, but also a specific amount of plain product needs to be run through the system before it is considered flushed. Progressor Sequencing tracks the total amount of qualified plain product through the process since the configured controlled products were used. Configured sensitive products cannot follow until the above criteria is met.
+ Hand-Add Interface
- The hand-add interface allows for manual hand-adds to be added via a connected scale. Weights are automatically recorded and added to the batch. Hand-adds can be weighed in advance for all runs that have been initialized in the batching run queue
- The touch screen display prompts for each ingredient. The target and actual amounts are displayed graphically and change colour as the target weight is reached and change colour to red if there is a tolerance alarm. Each ingredient must be acknowledged by the operator with a “Done” button before moving on to the next ingredient. Each weighment is monitored with over/under alarm functionality.
- If the target amount of a hand-add ingredient is greater than the configured full bag amount, the system prompts the number of full bags to dump and the balance is weighed on the hand-add scale.
+ Tote Bin Weigh Belt Scale
- High Capacity mode ( Xkg - Ykg )
- X is parameter
- Y is major scale capacity
- Resolution is resolution of major scale
- High Resolution Mode ( .2kg - Xkg )
- X is above parameter
- Resolution is resolution of weigh belt
+ Additional Features
- User friendly operator interface for simple and easy system operation and configuration
- Progressor Security provides full configuration of users and security levels
- SQL database
- 10 year database history with automatic data lifetime management
- Automatic batching for all batching augers, scales and mixer
- Scale instruments directly integrated into the PLC EtherCAT high speed network
- Liquid control for applying mixer liquids
- Multi-batching
- Simultaneously weighs from multiple bins with the same commodity.
- Substitution
- Allows a user with proper security login to substitute a different set of commodities to replace another commodity
- Quick primary bin select from “No Flow” message allows selection of a new primary bin without leaving the batching screen.
- High resolution Trending:
- Graphical visualization of individual batching auger performance
- Trending History allows trend graphs to scroll back in time
- Alarm and Status Logging for a history of system operation
- Reports
- Complete batch and run report database.
- Performance, usage and production reports.
- In addition to the standard reports, the Database is pre-configured with an IT connection to allow IT staff to extract custom data queries from the live production database, providing external access to all production data.
- Progressor Formula Import
- Electronically imports formulas from standard formulation software systems. Optional custom formula interfaces are available as required.
- Automatic Routing
- Product is automatically routed from the mixer to destination bins.
- Commodity interlocking is configurable based on Formula Code or Hash Code and ensures the product is automatically routed only to bins assigned to the product being processed.
- High level interlocking automatically routes to the next selected bin on a bin high level condition.
Pelleting
+ Pelleting Features
- Full pellet line automation for three pellet lines from source bins through pelleting, cooling, crumbling, screening, classifying, post pellet liquid and automatic routing to destination shipping bins.
- High performance pellet mill control enabling higher production rates
- User friendly operator interface for simple and easy system operation and configuration
- High resolution Trending Graphs for Target and Actual Temperature, Horse Power, Feeder Speed and Liquids
- Trending History allows trend graphs to scroll back in time
- Alarm and Status Message Logging for a history of system operation
- Pellet mill true Horse Power Control for accurate motor load feedback
- Horse Power Profiling for Superior Plug Detection and Reliable Automatic Recovery
- Fines Return Compensation for accurate liquid application and tonnes totalizing
- Liquid control for applying liquids at the conditioner, die and post pellet
- Switch between Auto and Manual on the fly
- Independent Pellet Type parameter groups for different formulas with varying pelleting characteristics
- Superior Proportional Control Algorithm for Horse Power and Temperature Control
- Superior Ramp Control to reach Target Temperature & Production Rate quickly without overshooting past target
- Volumetric control for consistent steam shut-off at the end of the run
- All liquid setpoints are extracted directly from the batching formula, eliminating duplicate setpoint entry.
- Commodity interlocking ensures the product is automatically routed only to bins assigned to the product being processed.
- High level interlocking automatically routes to the next selected bin on a bin high level condition.
- Cooler temperature monitoring for cooler product discharge, cooler air discharge and ambient air temperature. This allows cooler performance to be monitored and also includes high temperature interlocking to stop the fan to help prevent a cooler fire.
+ Progressor Pelleting
Progressor Pelleting automatically controls the entire pelleting process. Developed through many years of experience and extensive R&D, Camar has developed the high performance Progressor Pellet Mill Controller, which has demonstrated outstanding performance and substantial performance increases on every installation. All run parameters are recorded in the run report database, providing complete documentation for quality control and regulatory compliance. The Progressor Founding Principles are outlined below. We believe the results speak for themselves.
The Progressor Pelleting Founding Principles
+ Intelligence with Simplicity
Reliably controls the pelleting process like an intelligent operator would, but with greater consistency and with little operator attention. The operator interface is user friendly and easy to operate.
+ Fast Ramp & Temperature Control
Ramps up to target temperature and production rate quickly, without overshooting the targets, at the start of a run. This reduces the amount of off grade product, improving pellet quality and increasing pellet mill throughput.
After ramping, Progressor controls the temperature using its own new intelligent proportional control algorithm which supersedes the less reliable traditional PID loop control. Progressor intelligently relates and integrates all pelleting variables and responds accordingly, to maintain the temperature at target without cycling above and below target. This level of control intelligence allows the operator to enter the desired temperature and production rate targets then simply start the run and Progressor quickly ramps directly to the desired targets without overshooting. This increases the stability of the process and increases production and enhances quality control.
+ Stability
Stabilizes the pelleting process ( which is inherently unstable ) through intelligent control of the feed rate, horse power, steam and temperature to reduce the number of pellet mill plugs, while at the same time allowing increased production rates and improved product quality.
With TPH mode, the pellet mill is controlled based on production rate, not motor load. This eliminates system instability as a result of attempting to control based on a constantly fluctuating motor load.
+ Advanced Plug Detection
With its unique Horsepower Profiling method Progressor reliably, intelligently and automatically detects pellet mill plugs immediately, as they are developing, without operator attention, then quickly and automatically recovers from those plugs to maximize production. Typically plugs are detected and Progressor takes corrective action before the operator notices the plug condition. All of these features enable Progressor to reliably tread the fine line between maximized production and a plug condition.
+ Rugged, Industrial Reliability
Progressor is a Rugged, Robust and Reliable industrial control, built for the industrial environment of the mill. The entire control system, including the operator interface, is constructed of standard off-the-shelf industrial components.
tailored to meet our clients’ objectives
Stability
Because the pelleting process is inherently unstable, the Progressor stabilizes the process through control of the feed rate, horse power, steam and temperature to reduce the number of pellet mill plugs. This allows for increased production rates and improved product quality.
With TPH mode, the pellet mill is controlled based on production rate, not motor load, eliminating system instability.
Fast Ramp and Temperature Control
The Progressor ramps up to target temperature and production rate quickly at the start of a run, without overshooting targets. This reduces the amount of off-grade product and improves both pellet quality and pellet mill throughput.
After ramping, the Progressor controls the temperature using its own intelligent proportional control algorithm, which improves upon the less reliable PID loop control. Progressor relates and integrates all pelleting variables and responds accordingly to maintain the temperature at target without cycling above or below target.
Intelligence with Simplicity
The Progressor reliably controls the pelleting process like an intelligent operator would, but with greater consistency and minimal operator attention.
Advanced Plug Detection
With its unique horsepower profiling method, Progressor reliably, intelligently, and automatically detects pellet mill plugs immediately, even as they are developing. Without relying on an operator, the Progressor quickly and automatically recovers those plugs to maximize production.
Rugged and Durable
Progressor is a rugged, robust and reliable industrial control, built for the industrial environment of the mill. The entire control system, including operator interface, is constructed of standard off-the-shelf industrial components.
Easy Operation
The Progressor’s user-friendly operator interface allows for simple and easy system operation and offers the following features: high-resolution trending graphs for target and actual temperature, horsepower, feeder speed and liquids, trending history, and alarm and status message logging
Technical Intelligence
The Progressor features a number of intelligent systems to help refine each process, including pellet mill true horsepower control for accurate motor load feedback, horsepower profiling for superior plug detection and reliable automatic recovery, fines return compensation for accurate liquid application and production run totalizing, liquid control for applying liquids at the die or conditioner, easy switching between auto and manual, and independent pellet type parameter groups for different formulas with varying pelleting characteristics.
Progressor Routing
The Progressor’s optional Progressor Routing automatically controls the entire pelleting process from source bins, through pelleting, cooling, crumbling, screening, classifying, post pellet liquids, distribution to all destination bins and bin level detection.